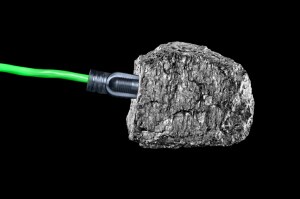
Bituminous coal is often used at power plants
A Utility Blending Application
In my last article, I discussed how on-line coal analyzers can help achieve proper sorting and blending of coal during the coal mining process. In this article I will discuss the advantages of a coal blending strategy at a power plant.
A power plant located in Pennsylvania illustrates how utility companies are applying tools to control coal quality, increase the availability of coal, and reduce the cost of generation without sacrificing boiler performance by blending low- and higher-grade coals.
Originally, this plant was constructed to burn a specific type of Eastern Bituminous coal that was in abundant supply and located in close proximity to the plant. In recent years, fluctuations in coal and emissions markets combined with dwindling availability of the design coal have caused the plant to consider burning alternate coals to reduce operating costs.
After considering available supplies, maintaining Sulfur dioxide (SO2) emissions within an acceptable range became a concern. [Sulfur dioxide (SO2) is one of a group of highly reactive gases known as “oxides of sulfur.” The largest sources of SO2 emissions are from fossil fuel combustion at power plants (73%) and other industrial facilities (20%). –EPA]
Their solution consisted of a new coal handling system including stacking tube stockpiles, an on-line coal analyzer, and an automated blending system. With these improvements, the plant has been able to increase coal supply options and still satisfy emissions requirements without any degradation in heat rate. The system optimized the economics of the plant by giving the power plant the ability to adapt to market changes in coal supplies, coal prices, and allowance markets.
Download 1+1=3: More from Your On-line Coal Analyzer and read how mining operators and power plant owners alike are improving their bottom lines with on-line coal analyzers.
[…] Next article: The third real-life example — coal-blending strategies at a power plant. […]